Our commitment
Our goals are simple: everyone who wants to run is welcome to run, and everyone who runs has a place to do it.
Our priorities
Putting one foot in front of the other starts here. These five focuses set us on the path to making real and lasting change.
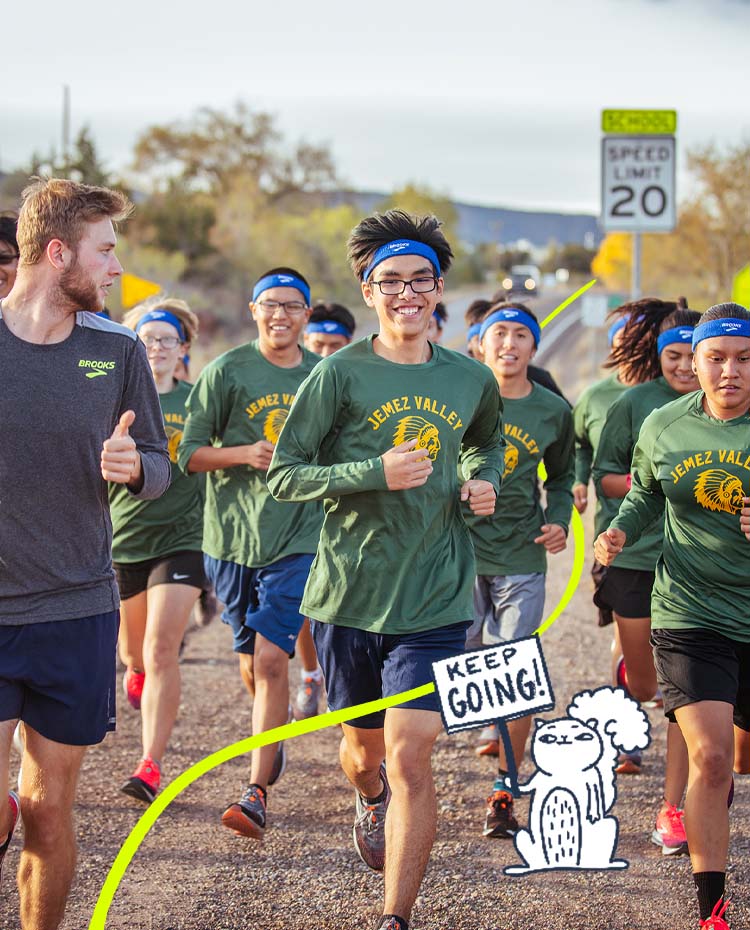
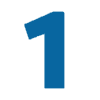
Diversity, Equity, and Inclusion
Reduction of barriers to participate in the running industry, on the run, and in the running community.
Learn more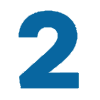
Responsible sourcing
Partnerships with factories who share our objectives to trace our supply chain, respect human rights, and reduce environmental impact.
Learn more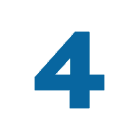
Sustainable consumption
Converting to recycled or bio-based materials, eliminating footwear manufacturing material waste sent to landfill or incineration, and launching a circular product.
Learn more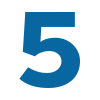
Community impact
Partnerships to advance health and well-being in our communities and make the run open to all.
Learn moreIt’s time to think big
We’ve charted our People and Planet Path to support the United Nations 2030 Sustainable Development Goals (SDGs). We are targeting the four SDGs where we feel we can have the greatest impact.
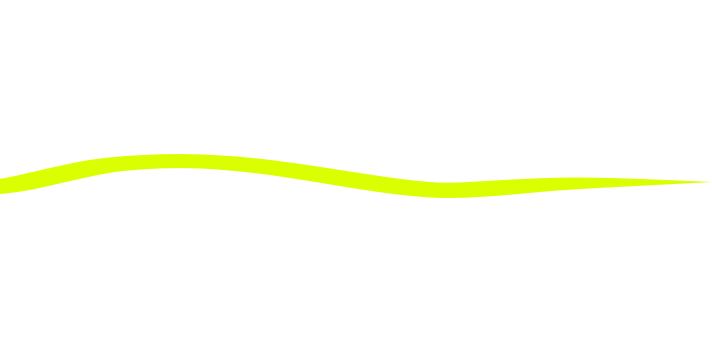
Where the rubber meets the road
Here are some of the most recent tangible steps we’re taking on our People and Planet Path.
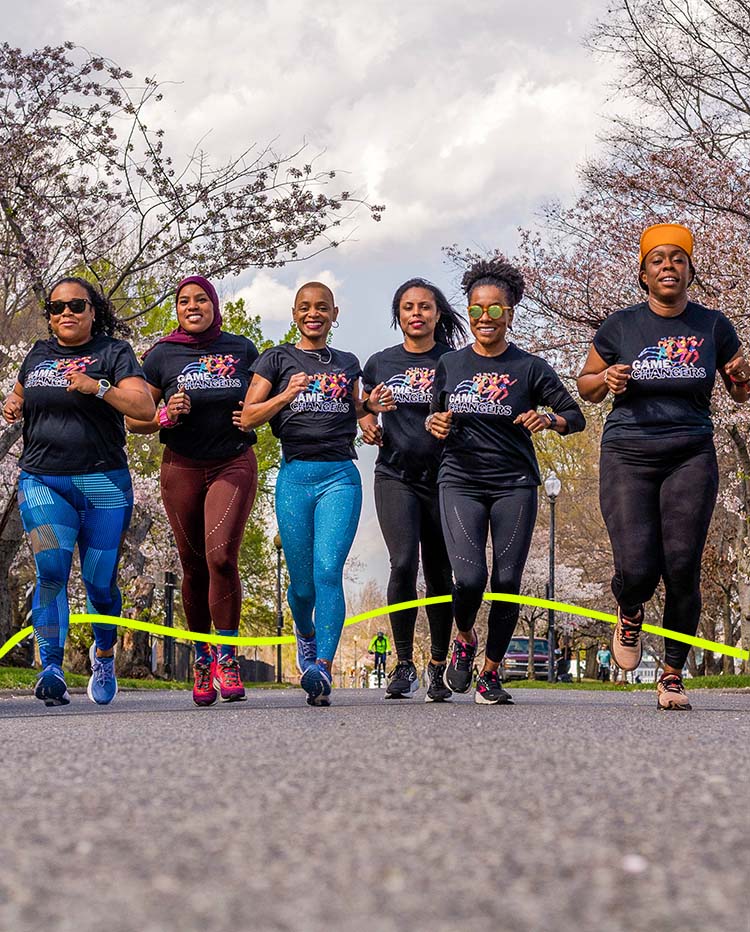
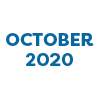
Running Industry Diversity Coalition
Dedicated to industry-wide BIPOC representation and access.
Learn more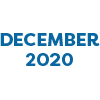
The Climate Pledge
Alignment with the international community on addressing climate change.
Learn more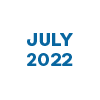
Recycled Materials
Incorporating recycled polyester and recycled nylon yarns into our product.
Learn more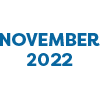
Carbon Neutral Ghost 15
Carbon neutral through reduced emissions and independently verified offsets.
Learn more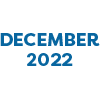
Updated GHG Reduction Targets
Near-term and net-zero targets validated by the Science-Based Target initiative.
Learn more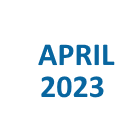
Business Coalition for the Equality Act
Working to pass the Equality Act to ensure comprehensive protections for LGBTQ+ people nationwide.
Learn more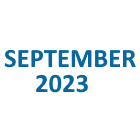
Green Silence Ghost 15
The Green Silence Ghost 15 is a step on our path to net-zero greenhouse gas emissions by 2040, and showcases over a decade of innovation.
Learn more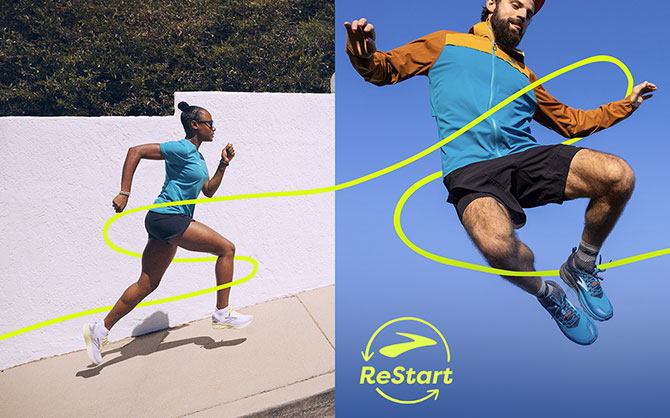
Gently used shoes for the long run
Brooks ReStart helps our gear stay on the run as long as possible, offering gently used shoes that still have plenty of miles left to go.
Transparency and accountability
The finish line of this marathon is a long way off, but we’re committed to positive change and transparency about where we can do more and how we can do better.
-
Our People
-
Our Planet
-
Our Purpose